SCADAScope
SCADAScope is like having an experienced troubleshooter sitting in the turbine 24×7, waiting to answer a phone call to help with operation from before the fault has occurred and until the asset is back in full production.
SCADAScope is ready to help you reduce downtime and optimize labour, by
- Helping your crew fix the problem the first time.
- Providing remote quality monitoring.
- Providing ready insights and quick root cause investigations
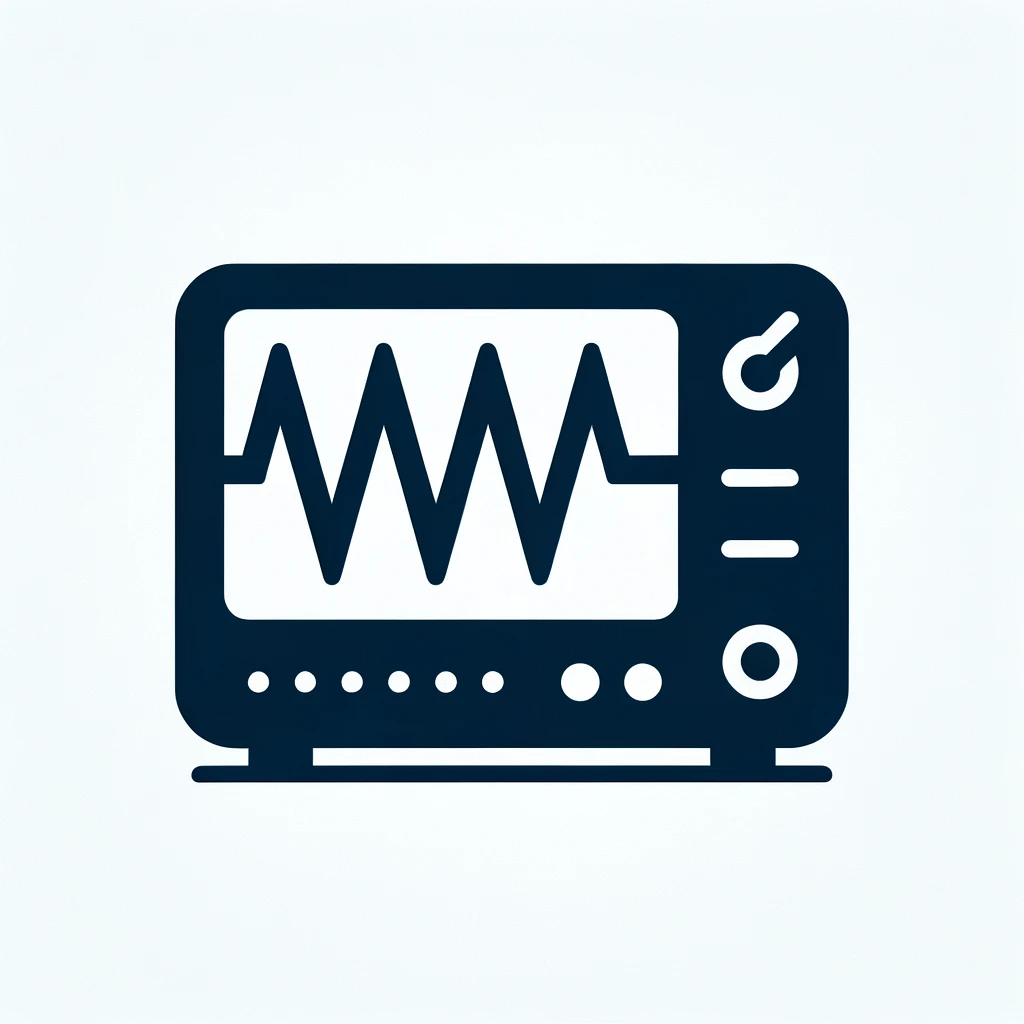
Rotor Balance
SCADAScope Quality 365 monitors rotor blade weight and aerodynamic balance continuously without any added hardware or stopping the turbine.
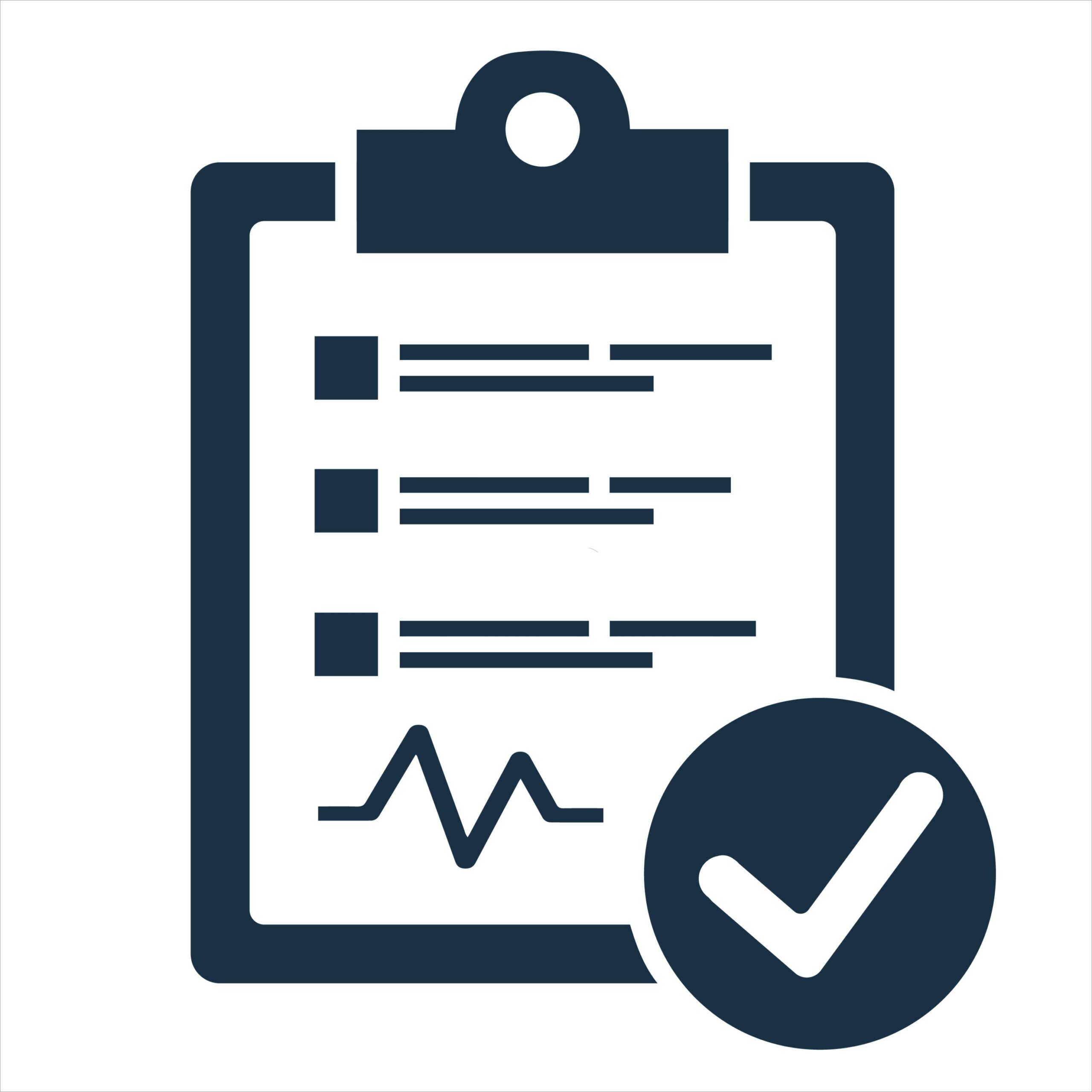
Yaw & Anemometer Misalignment
Quality 365 report identifies turbines with misaligned anemometers (Yaw Misalignment), and that increases AEP and reduces main bearing damage.
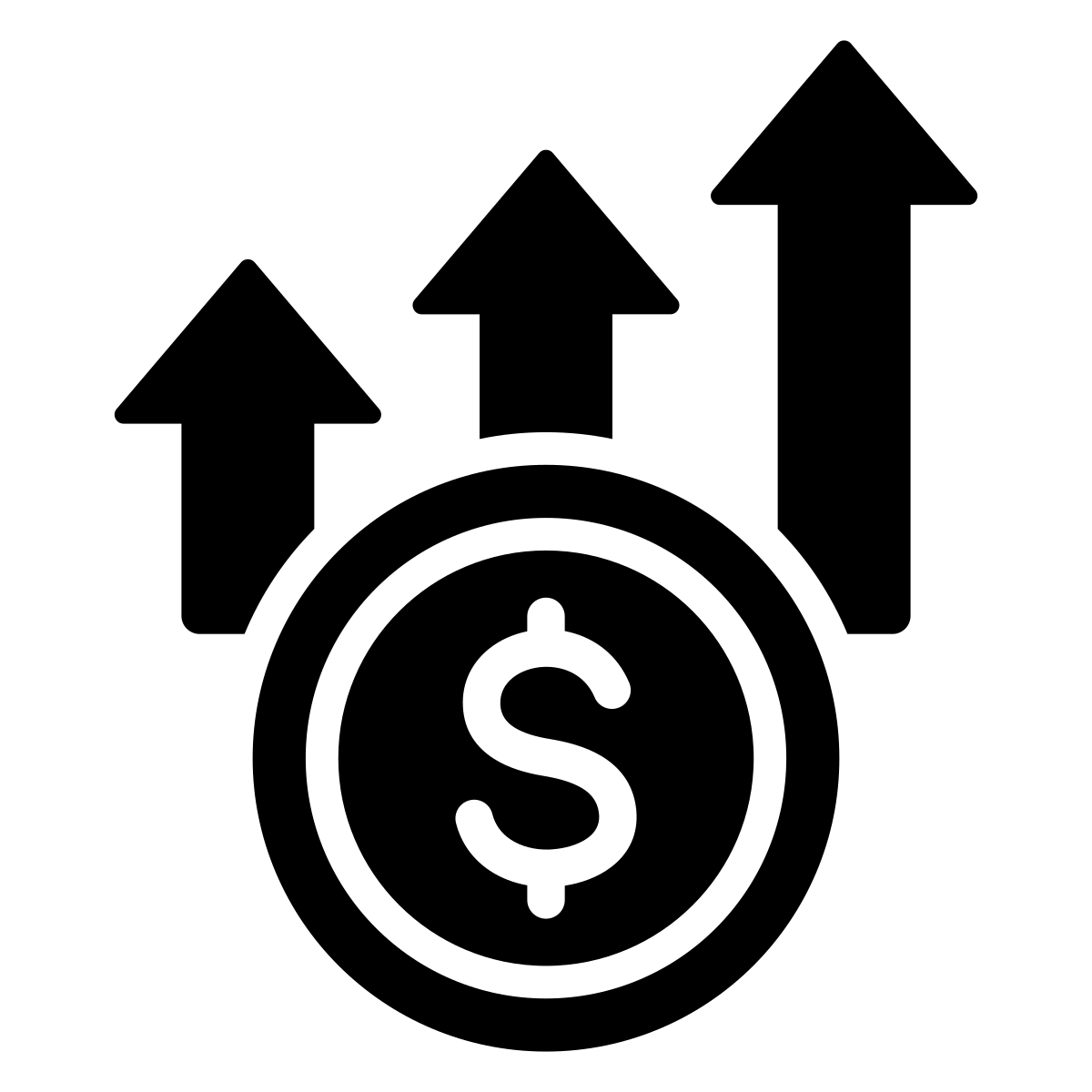
Prop Valve Issues
SCADAScope would identify pitch system problems that would cost you AEP and go unnoticed for years.
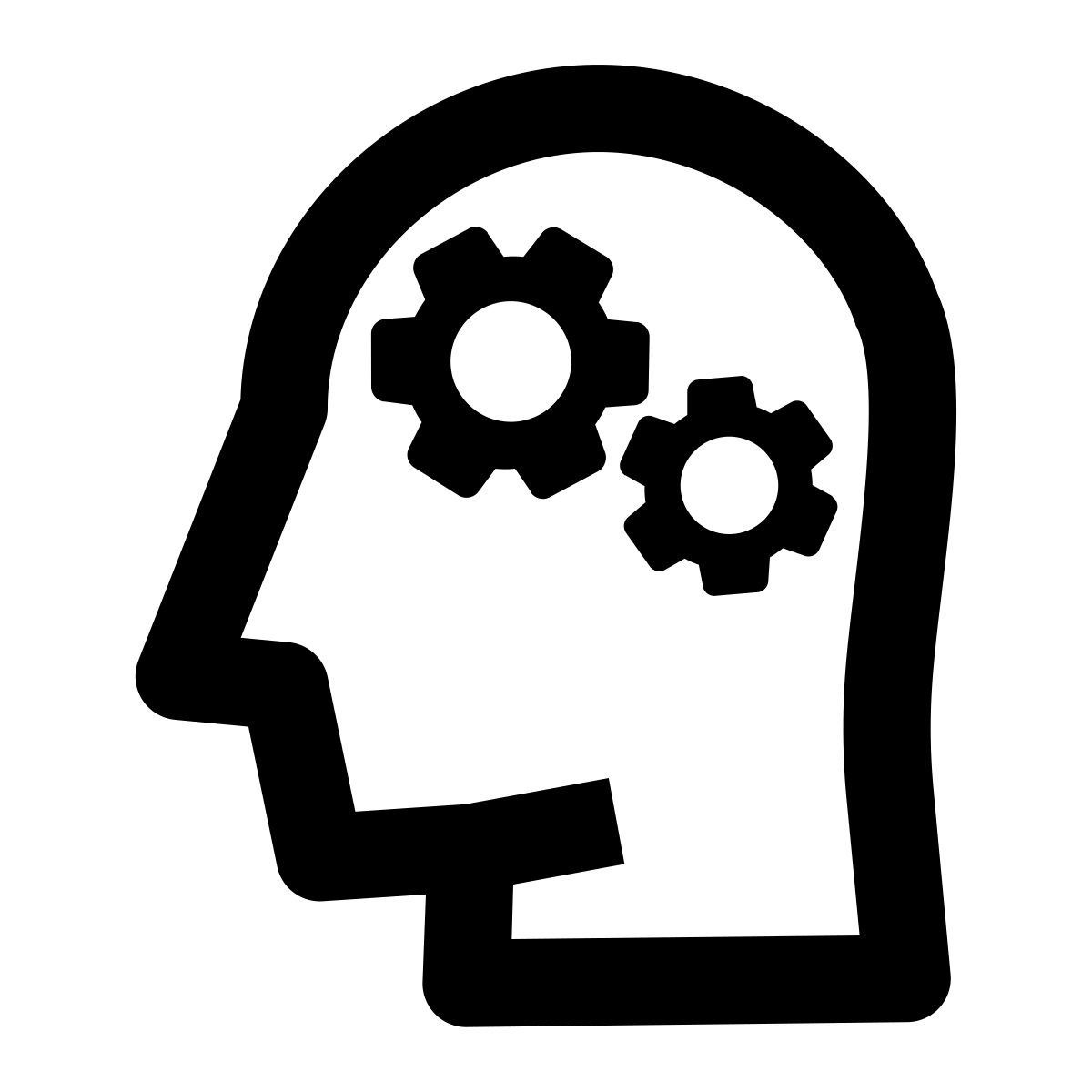
Troubleshooting Notes
Uptime 911 TSNs are the industry’s first data-assisted troubleshooting system with integrated self-learning.
SCADAScope captures high frequency data directly from the controllers and uses it to diagnose problems and perform analytics to reveal the condition of components.
For perspective, OEM SCADA gives you some value, let’s say the pitch angle of blade 1, every couple of seconds. Unfortunately, no one really knows how many seconds ago that value was actually reported by the turbine, or how long the SCADA took to relay that value.
SCADAScope reads directly from the turbine, as fast as values are available in the controller. When it comes to diagnosing problems of determining blade balance, this better data significantly improves the quality of results.
It does not and that is intentional. We designed SCADAScope to only receive turbine data and not interfere with its control and functionality.
That is a task for your SCADA.
SCADAScope can handle as many assets (turbines or solar inverters) as exist at the site.
For sites with a large number of assets or complex networks, multiple servers at different locations might be needed, but this is something we are prepared to handle.
Yes, absolutely. All the data collected by the system is available to the owner and kept for a minimum of two weeks so your historian can collect it from SCADAScope.
If you would like us to add a long term storage, we will install a separate server on site to archive the data indefinitely.
We can provide high value operational data from Vestas turbines, Gamesa and SGRE Offshore turbines, and IngeTeam systems. And we are developing data acquisition systems for ABB converter and GE turbines.
If you are not managing the day to day operation, then the value of SCADAScope is knowing if you are getting appropriate value from your assets and if they are being well maintained.
Also, the data is extremely valuable if there is any warranty claim. It’s fact on paper, and gives a lot of leverage to you when you know you have a case and you’re being stonewalled.
Yes. SCADAScope was designed from ground up to help you automate your operational expertise. If there are particular things you want to watch, SCADAScope is possibly the easiest system to leverage your inhouse knowledge.
We were keen on making a useful tool that helps operation. Fortunately, with the fidelity and resolution of the data, most problems can be found without AI. However, if we ever run into a problem suitable for AI, the modular and configurable nature of SCADAScope makes integration simple.
SCADAScope goes directly to the asset, and is independent of the OEM SCADA or the substation SCADA.
Uptime 911
There are a lot of systems that notify you of a problem. SCADAScope Uptime 911 is the industry’s first system to help solve problems.
Finding problems is awesome, Uptime 911 helps you solve them. Its sole job is to reduce the MTTR, the mean time to recovery. It helps your techs get problems fixed faster in as few visits as possible.
A normal OEM SCADA is like a Check Engine light in your car. It mostly tells you something isn’t working; SCADAScope is like an intelligent diagnostics system that tells your mechanic what the real problem is and where to start looking for it. It helps find the real underlying causes and distinguish them from secondary effects.
SCADAScope is designed from the ground up around one intent: solving problems that actually ruin someone’s day. And this is very apparent in its ready-to-use Troubleshooting Notes (TSNs) that are sent out for faults to help the crew fix it right the first time.
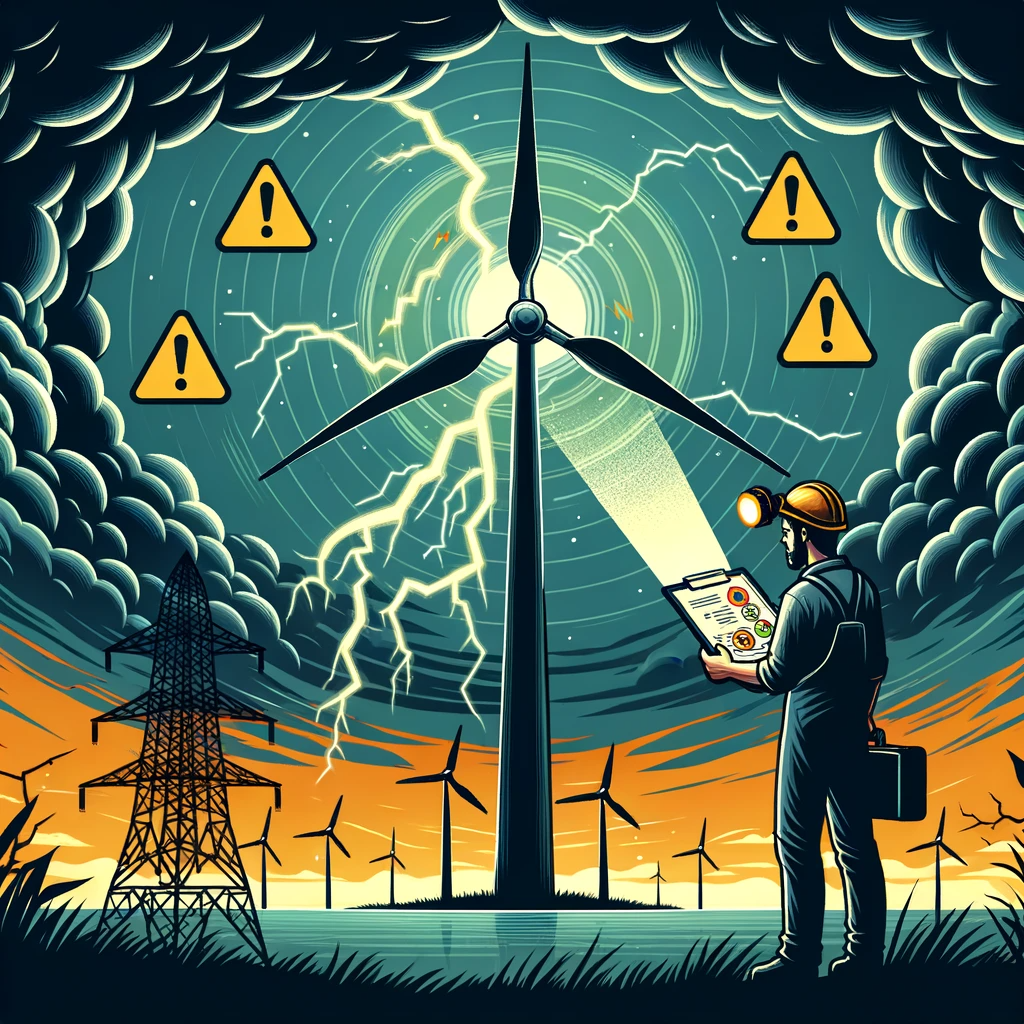
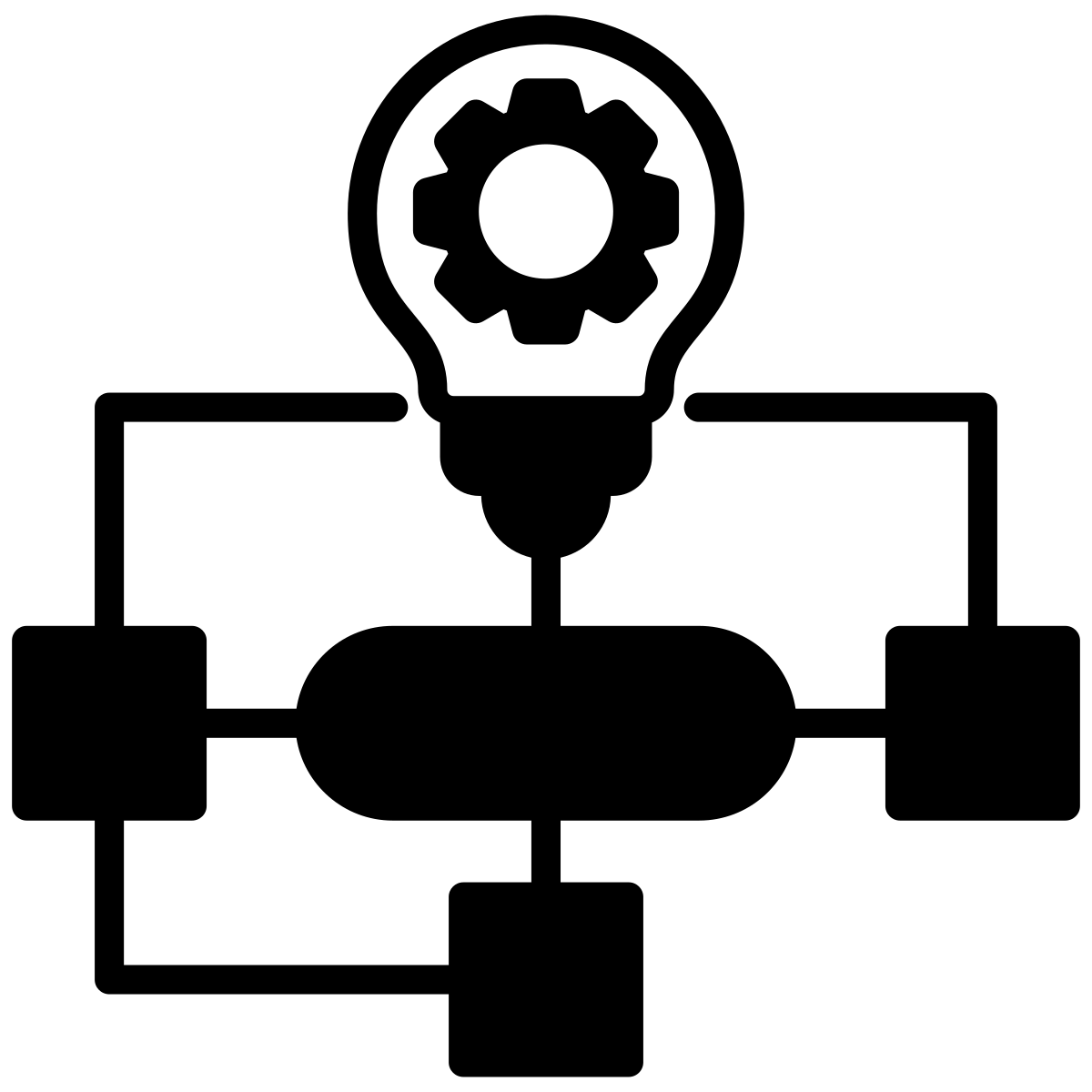
Schematics Included
Troubleshooting Notes for electrical problems contain relevant pages from the schematics with the problem areas highlighted.
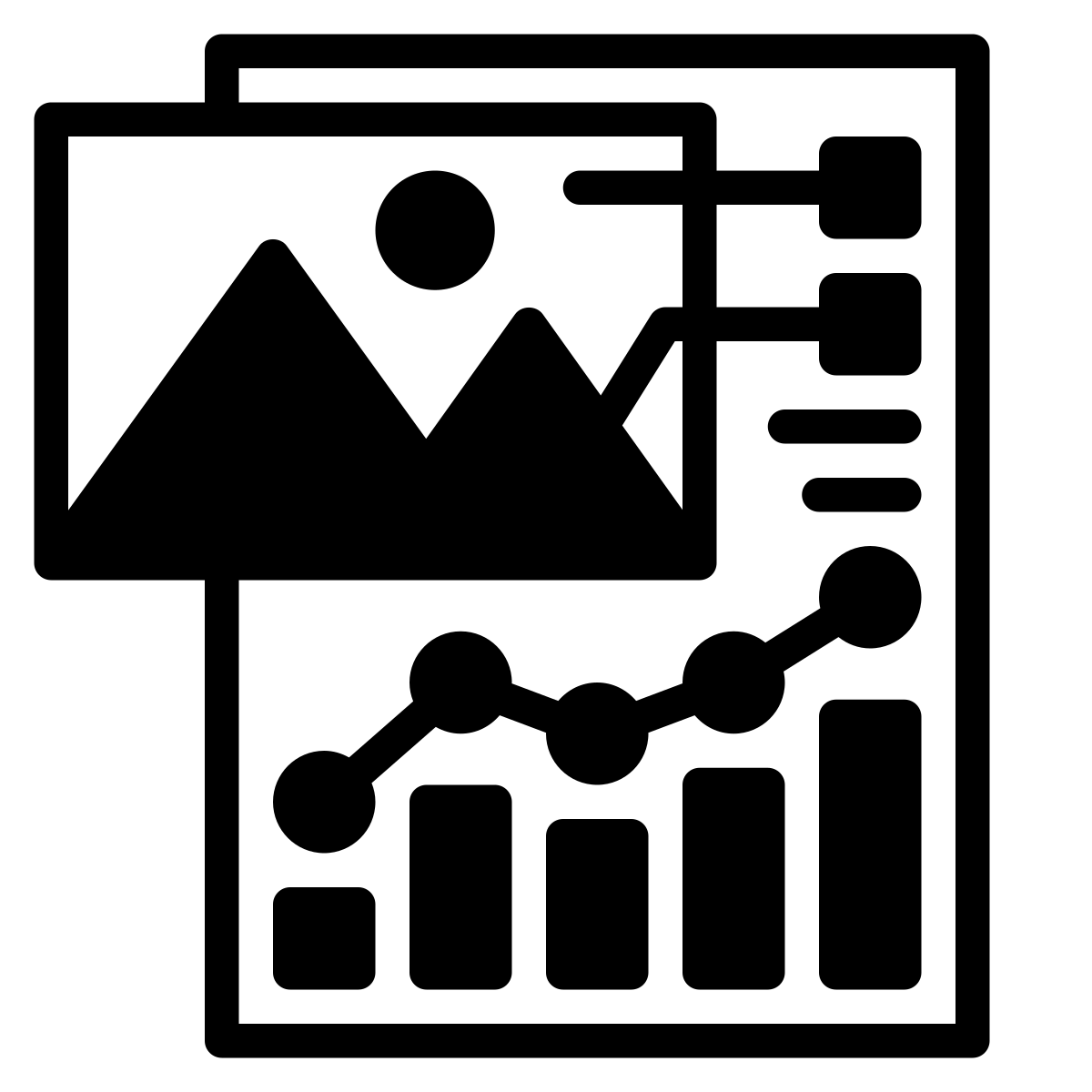
Guiding Images
Photos of components help technicians look in the right place by familiarizing them with the right components.
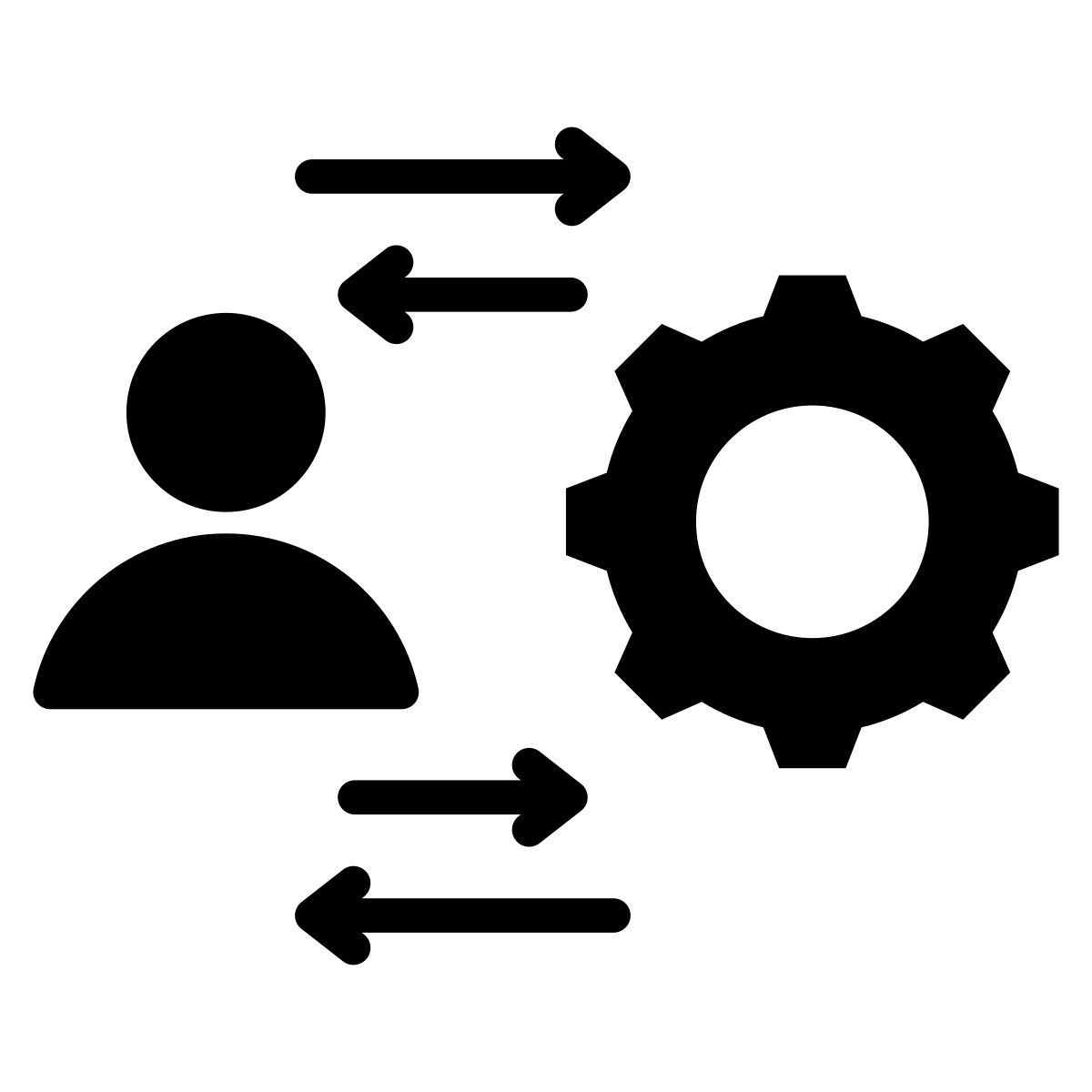
Fault Evidence
Uptime 911 TSNs contain the high resolution fault data of the signals that tell the best story available to help the right team approach the problem with the right parts.
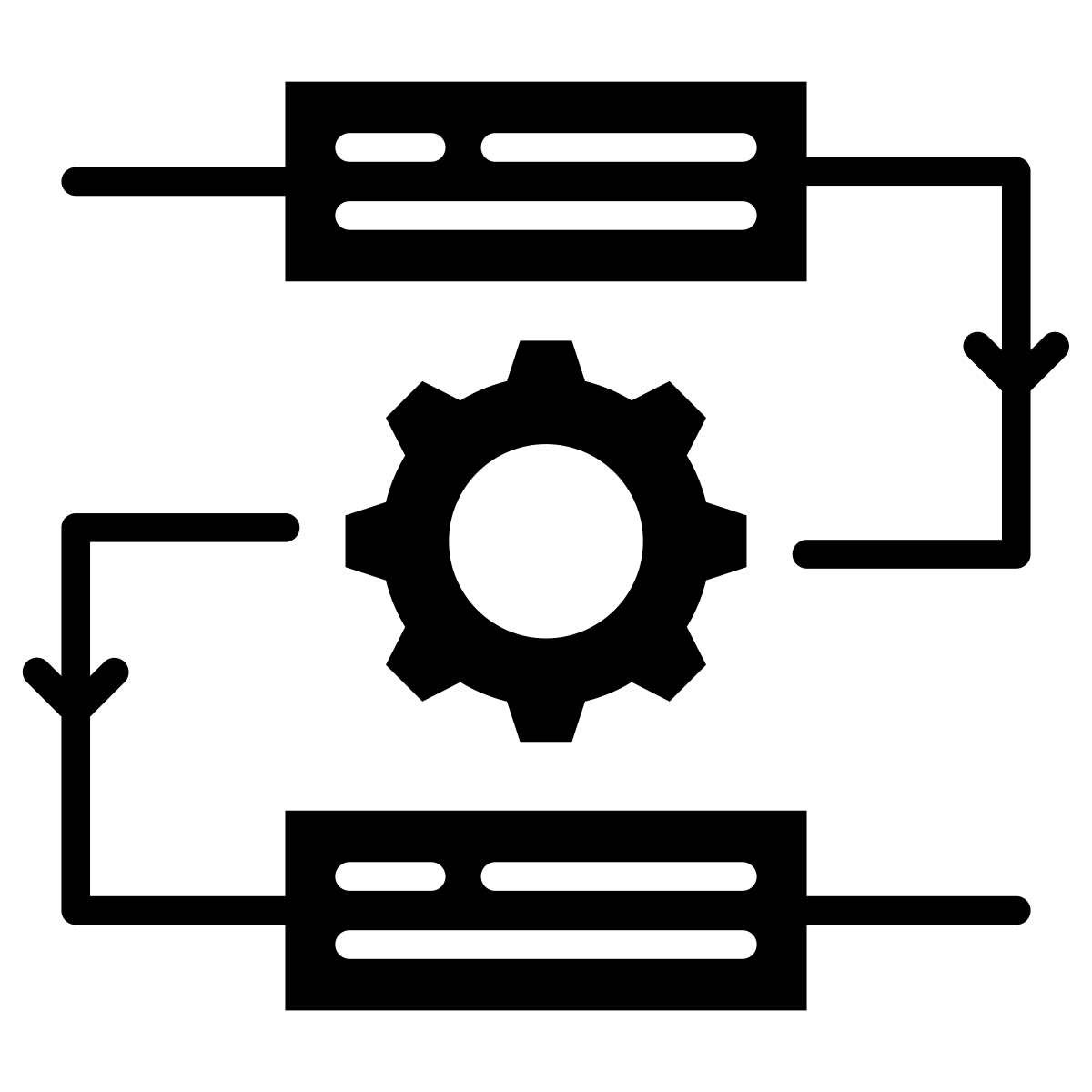
Ever Improving System
Every time a problem is found and photos of the defective part or connection are sent back to SCADAScope, it helps the next troubleshooting get easier.
When an asset is down, SCADAScope helps your crew know where to go and what to look for?
Before the crew leaves for the turbine, they are equipped with a Support Ticket that would help them:
- Get the right spare parts
- Have the right tools ready
- Know a good place to start
- A list of tests to perform or general questions answer
No, it is not designed to manage work but only to identify and guide the work needed, SCADAScope TSNs contain the most crucial information to go into a work order without being a work order
It could, however, feed into a work order system (ERP) and there are a lot of excellent ones out there. AP could help you get one connected, or get one deployed. We regularly add new interfaces for new work order systems (ERP, SAP, Salesforce, Excel, Access, etc.)
Uptime 911 TSNs are designed to help with every problem that SCADAScope has good data about. Of course certain events happen without a clear signature but SCADAScope helps you establish the sequence of events from the PLC point of view and find the main event that led to stoppage.
Overspeed systems (e.g. OGS, VOG, Aero brakes) often have independent controllers that are not directly recorded. But the high speed data from SCADAScope gives you the ability to find the problem, even when data is missing from other devices.
SCADAScope data answers a very critical and time saving question: Was there actually a safety event (e.g. An overspeed) or did the safety system malfunction?
Quality 365
While Troubleshooting Support helps you put the faults behind you, Quality 365 will keep you ahead of the problems. As good operators say, you are winning if you set the plan of the day, not the turbines.
Quality 365 is there to prevent failures and increase the mean time between failures. Its job is keeping the machine running longer before it needs another visit.
It does this by ensuring the quality of maintenance and revealing hidden problems.
Some people call it Condition Based Maintenance. We call it knowing exactly what needs attention and ensuring that the maintenance is done right.
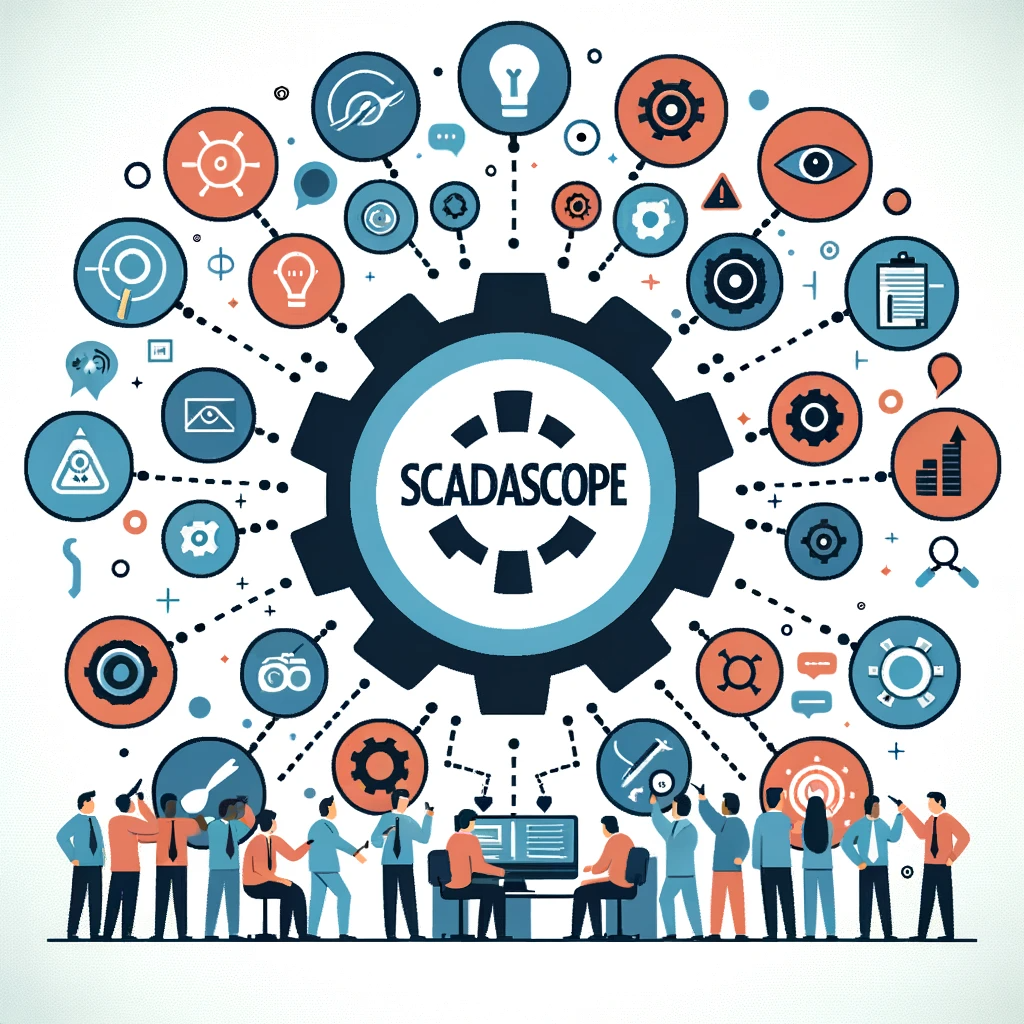
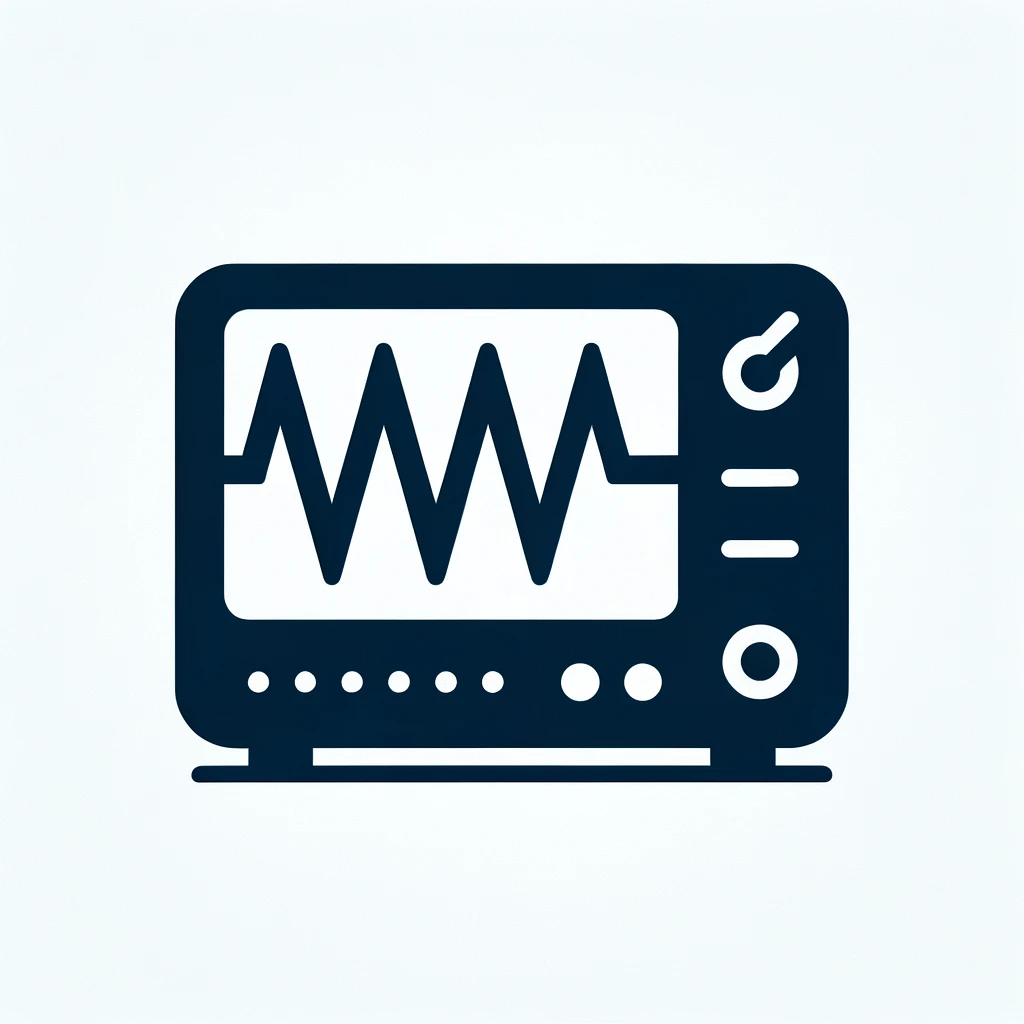
Continuous Monitoring
Quality 365 is a qualitatively higher level of risk reduction, every day. It is running whenever your asset is running (and even when it stops running).
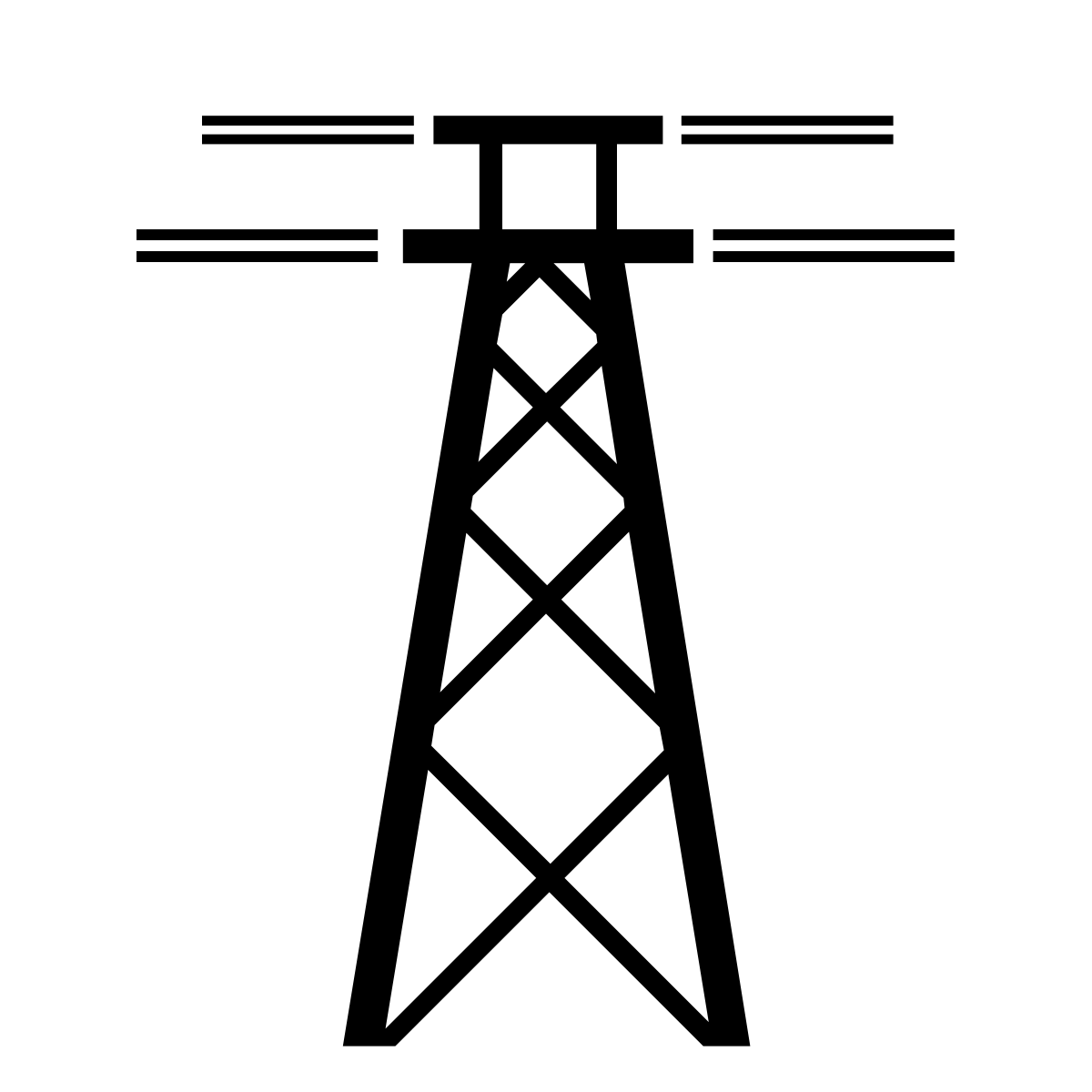
Grid Support
It’s a lot easier to keep on top of auxiliary components that help the turbine support the grid with a remote audit that highlights any major deficiencies.
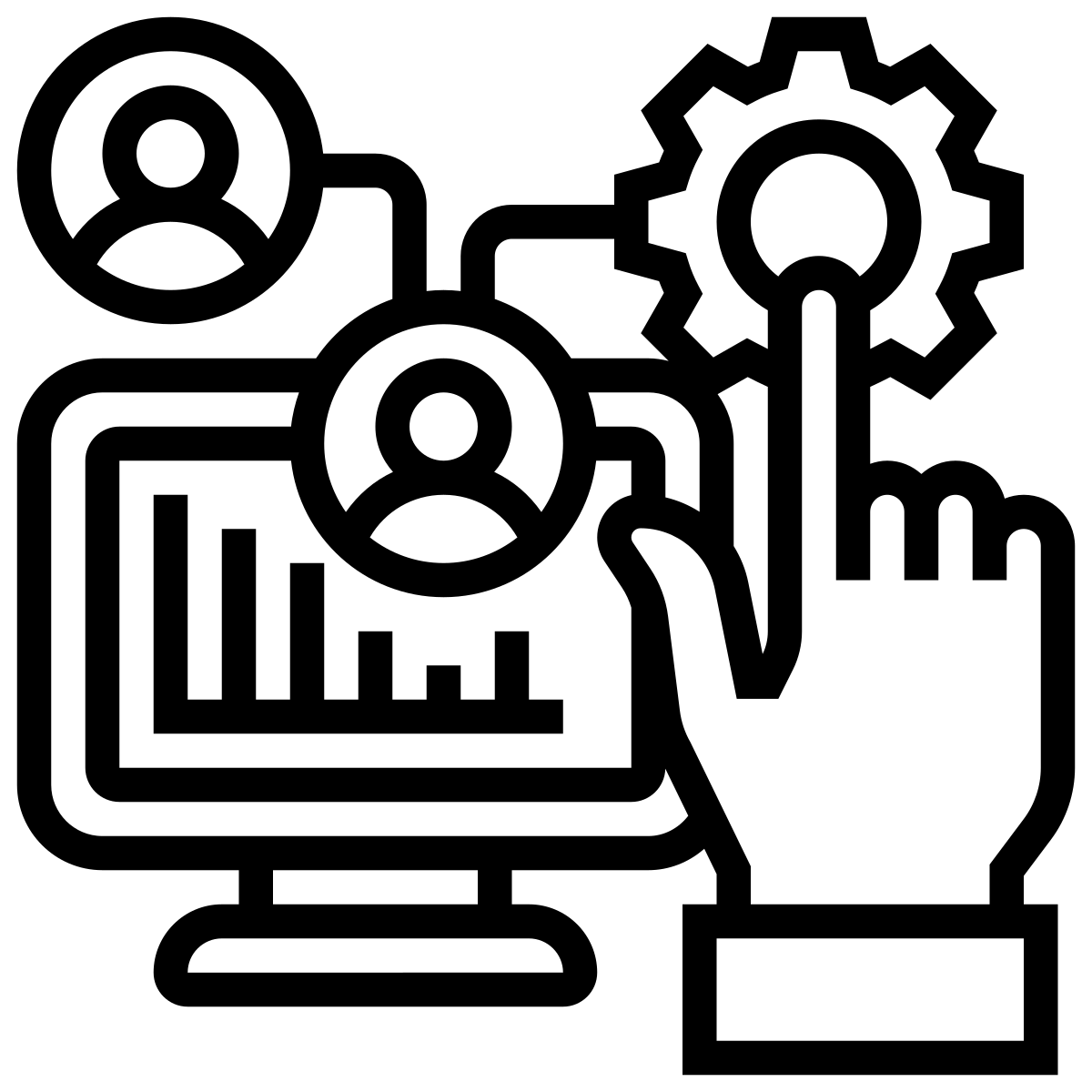
Preventive Planning
Quality 365 helps you plan your preventive actions by highlighting what needs most attention.
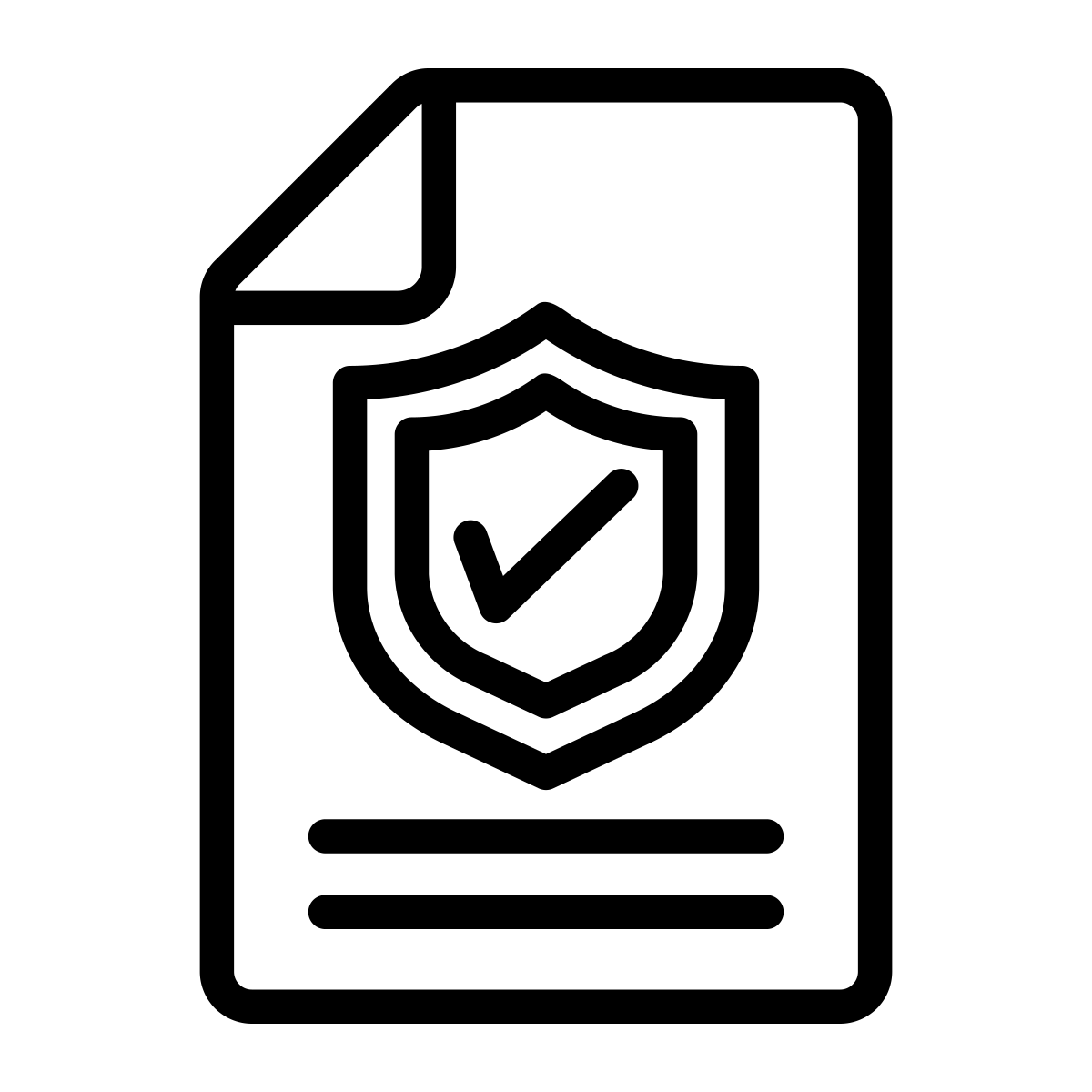
Preventive Quality
Quality 365 remotely audits key aspects of the preventive maintenance to track and trace quality deficiencies without the need for physical inspection.
The quality report is useful for a quick comprehensive cheap scan of the site without ever getting dust on your boots.
- Blade & Rotor balance
- Pitch system
- Yaw system
- Transformer cooling
- Gearbox cooling
- Gearbox vibration (G8x only )
- Generator cooling
- Yaw misalignment
New features and components are added regularly.
As often as you like and as often as it helps you optimize your planning.
Some of the quality KPIs need a few days of data, so we don’t think checking it every day would tell you anything new.
If there was an urgent problem, and it was fixed, there are other ways to check for it. For example, A single Support Ticket could tell you if the rotor balance on turbine 55 was fixed.
Yes, based on your contract, we could schedule it and our team would send it out as agreed.
Root Cause Analysis Services
You should not need to wait quarter after quarter for answers to problems that cause everyday concerns. Owner investigations and engineering RCAs regularly run into delays caused by lack of data and cooperation by the suppliers. That’s why we help you go beyond the OEMs by starting with high resolution data.
Sometimes the problems affecting the P&L go beyond everyday troubleshooting and maintenance. Construction, legacy engineering issues, design defects, warranty issues, software problems and complying with new regulations are some of the more systematic problems that could impact the bottom line.
Our root cause analysis services using the SCADAScope high resolution data, along with our domain expertise in the target platforms shortens the time to final results and is a high value pathway to accelerate your strategic decisions with hard evidence and strong analysis.
Our Root Cause and Insight reports can be useful to you if you have specific questions about an issue that is happening or want more detailed forensics done. It starts with your operation and ends with a systematic analysis of the data available from the controls at your plant.
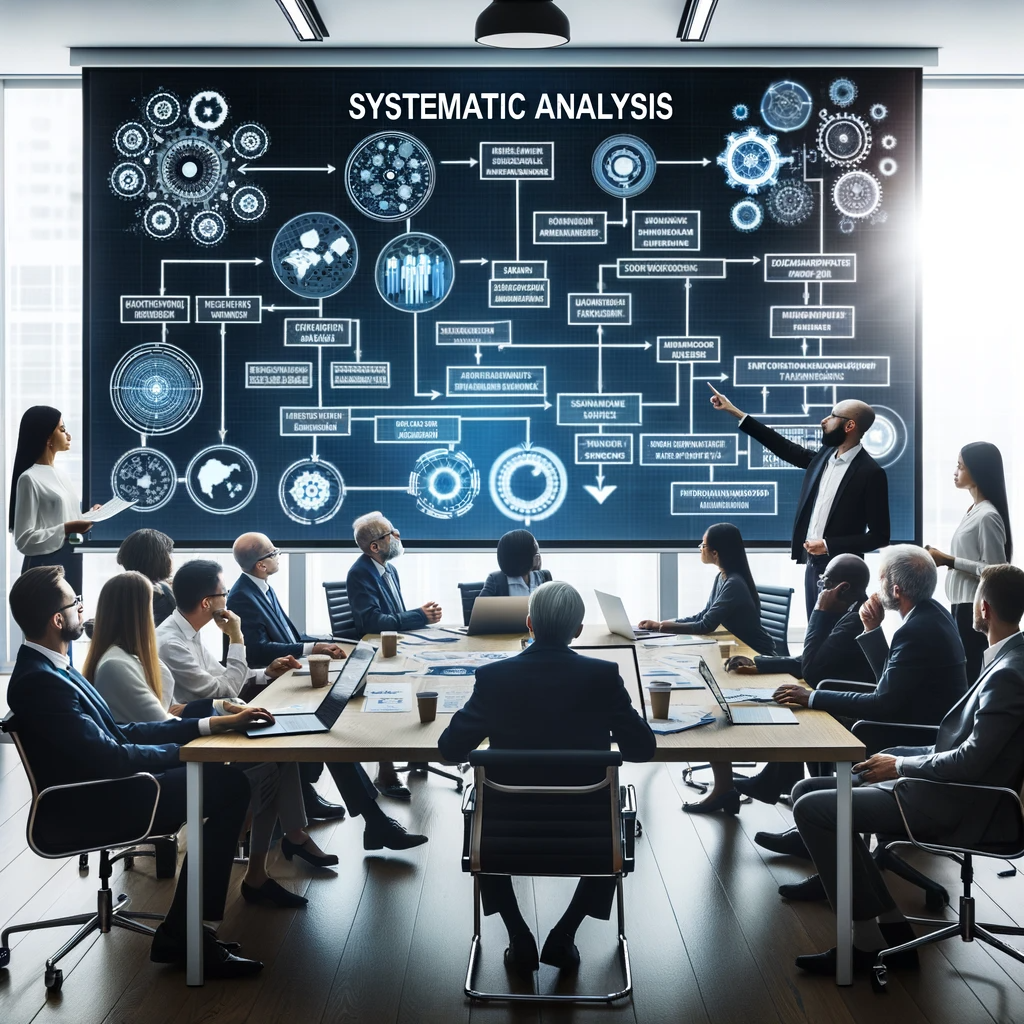
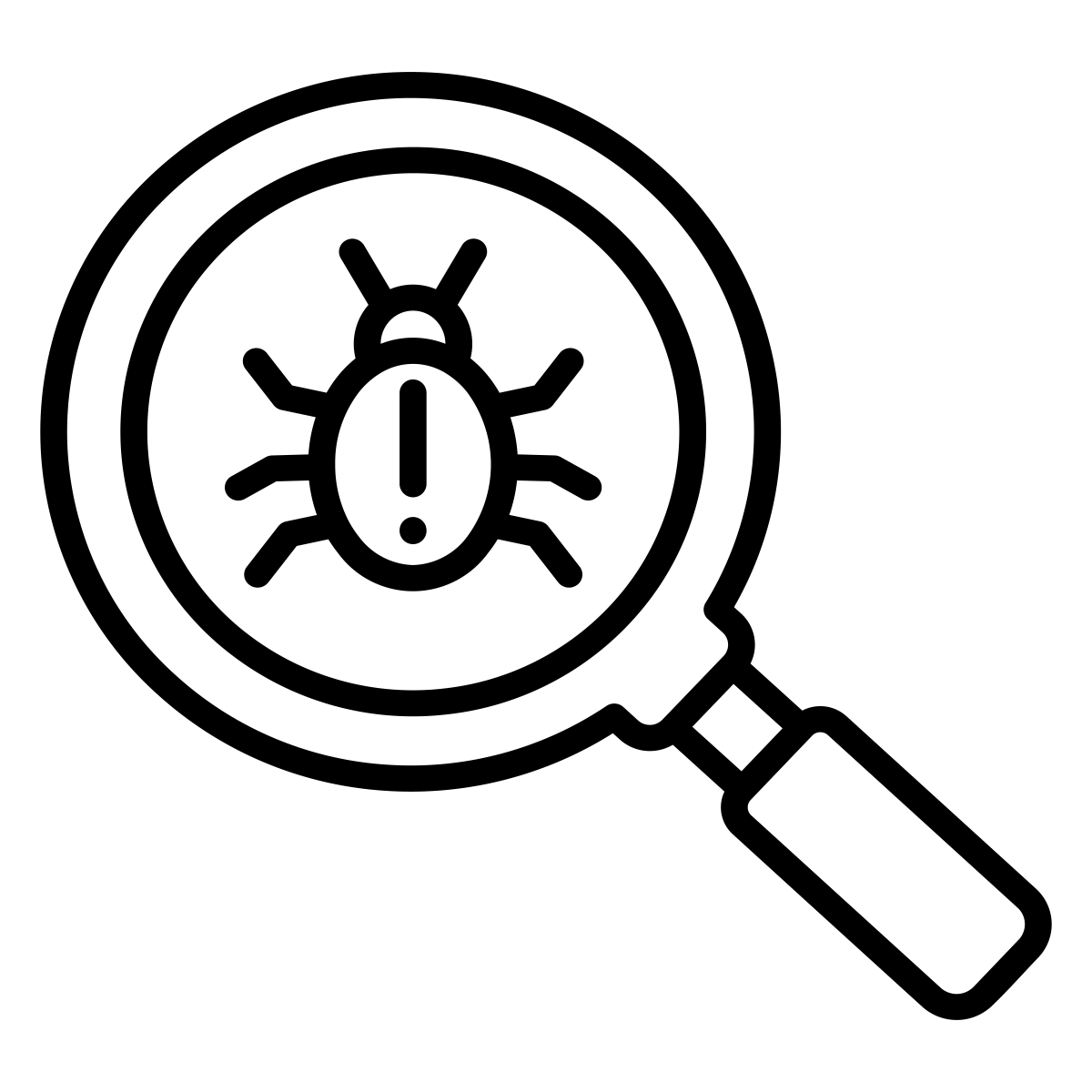
Find Software Bugs
Identify software issues and capture fault evidence.
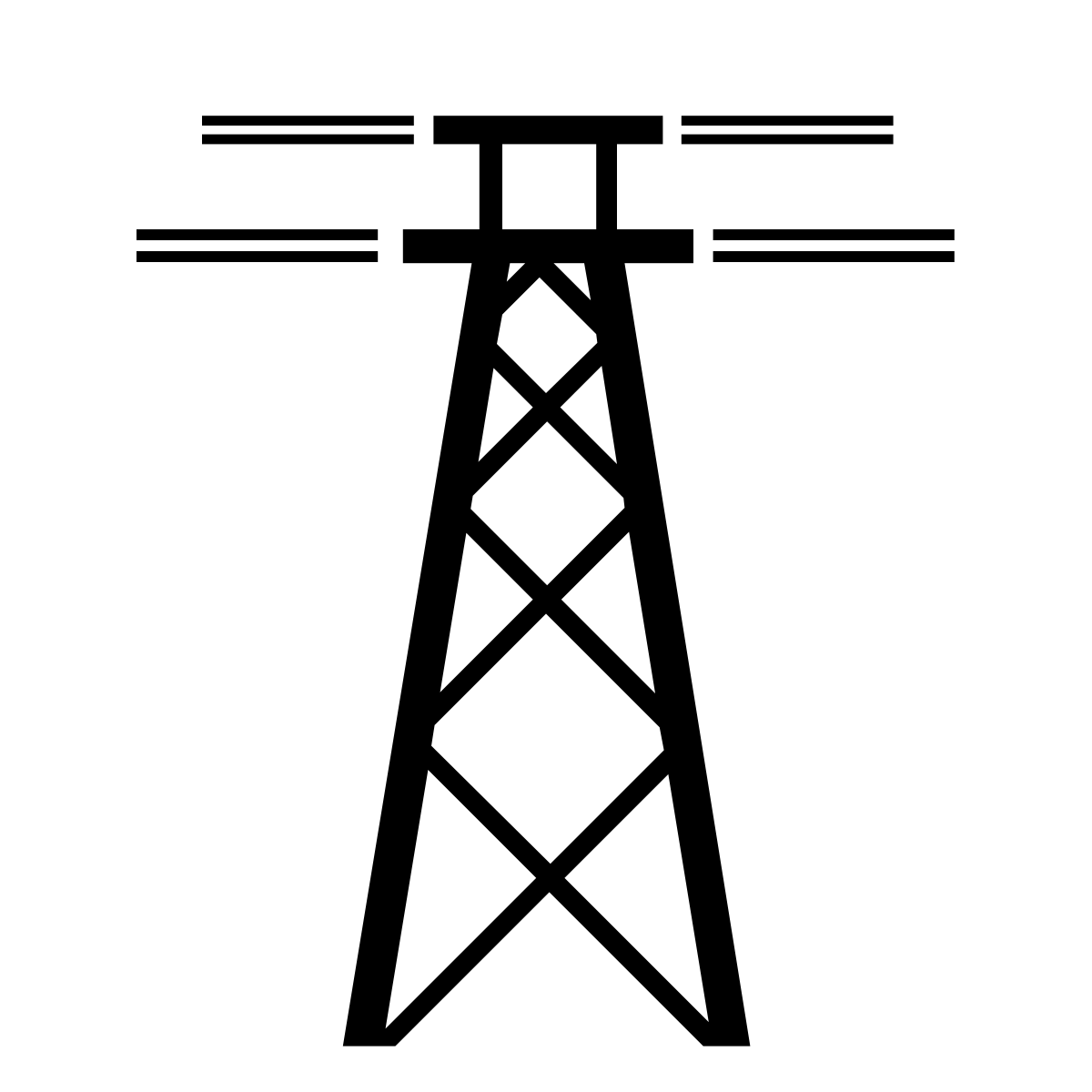
Grid Compliance
Ensure your asset performs as intended and be ready for grid changes.
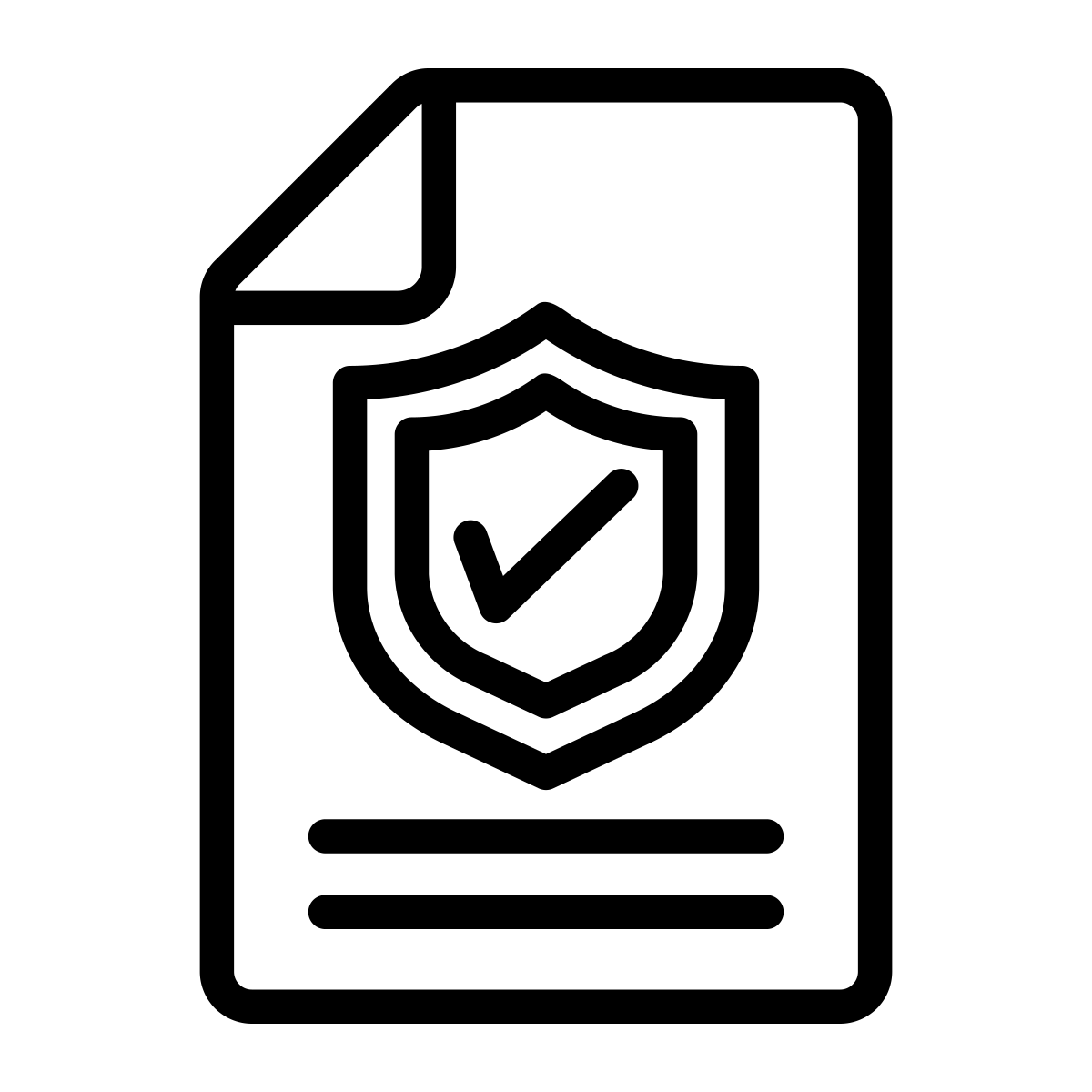
Warranty Claims
Approach warranty concerns methodically with high definition data and best industry support behind you.
For example, if you have a grid problem or a lot of unusual valve failures, our services can help point you in the right direction, allowing you to fix the problem faster and improve your P&L.
For warranty claims, most of our clients love having data that can back their claim. They never told us how much it saved them, but the smiles are telling.
When there is a chronic problem or there is a question that requires a deep dive into the data, you reach out to service@aprenewables.com and we work with you to make sure we have all the relevant information about your issue, and then our engineers generate a report addressing your issue.
This is a customized service and we first assess the value and make sure the problem that’s being taken on would have signatures in the SCADAScope data.
If you have concerns about the latest software causing new unwelcome things, this is the way to detect and prove it.
Raw Signal Data
It’s your asset and you should not be prevented from accessing any data you want from it, for whatever reason that might be. SCADAScope gathers data from your assets where you can look at it in the web viewer, or gather it into your historian over FTP or a HTTP API.
SCADAScope DA modules (the Data Acquisition parts of the system ) connect to different controllers in each asset and store this data for downstream analysis by other SCADAScope modules and make it available
Sometimes human observation of the data is far superior to automated issue detection, especially when the cause is new or the problem unfamiliar. To allow ease of viewing and selecting appropriate data, we made the SCADAScope Grapher.
SCADAScope Grapher is a web based tool which allows you to graph the required high frequency data from the turbine over the appropriate time.The Grapher provides your subject matter experts with a window into the most detailed form of the raw data.
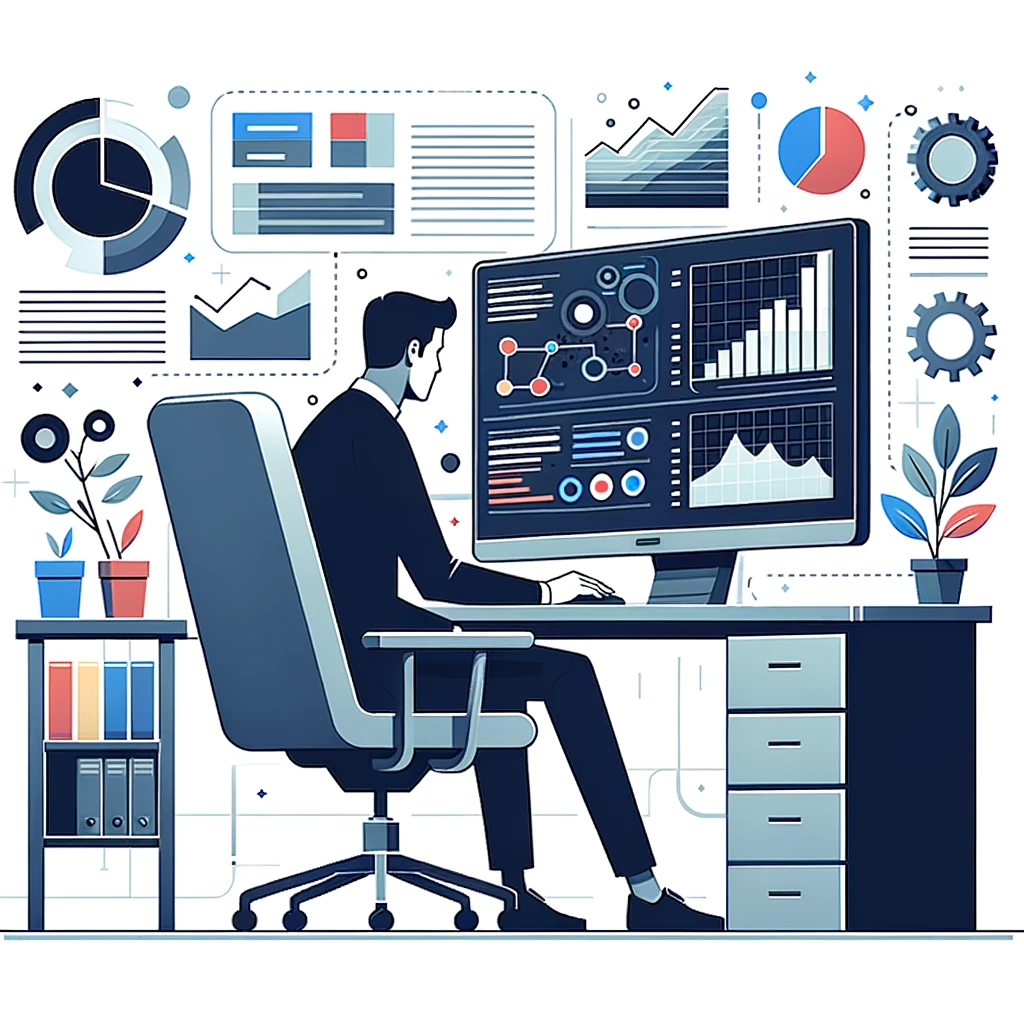
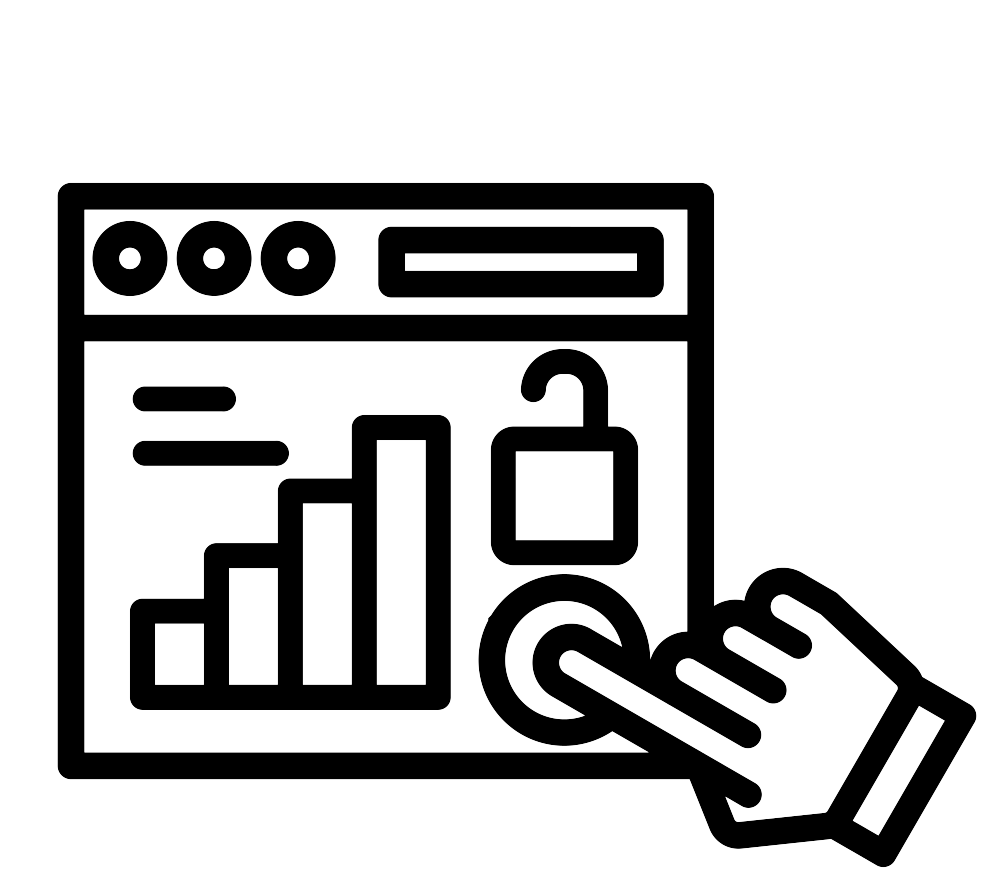
Easy to Use
Our methods for storing the raw signal data make it easy to access and use in other systems.
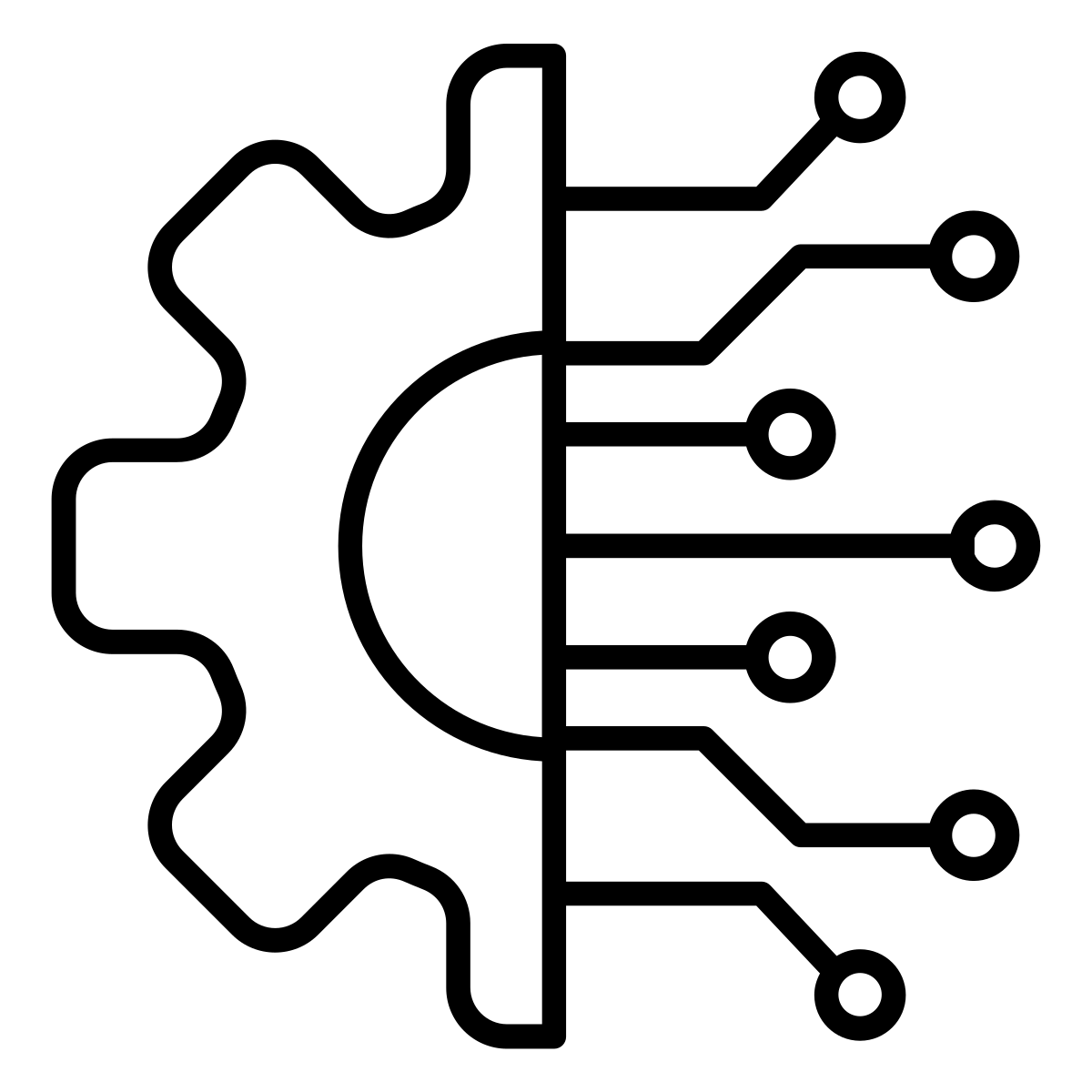
Digital-Twin Ready
High resolution data enables dynamic modeling, or making of a digital twin without any new hardware
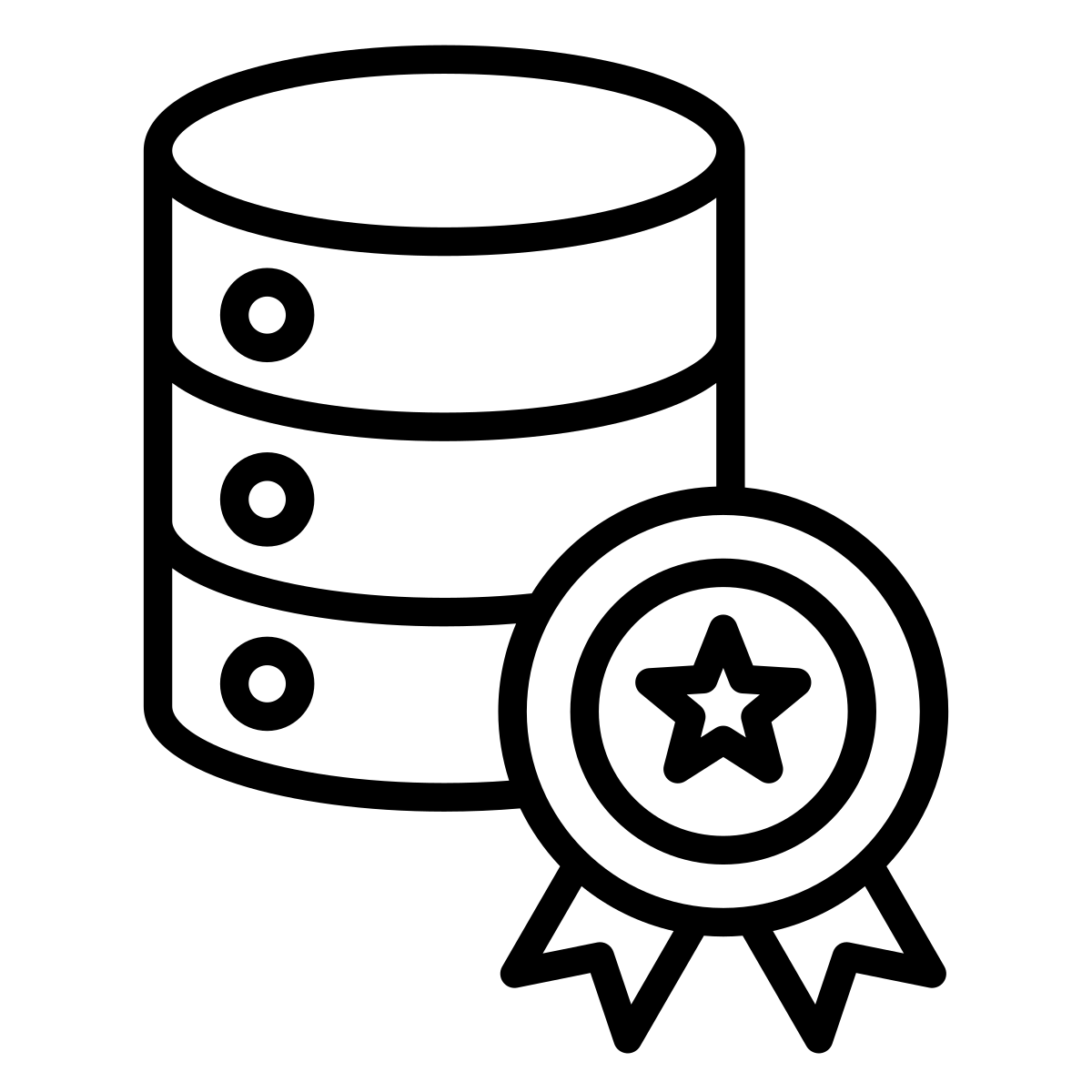
High Frequency Data
Enable fault tracing and signature detection by accessing higher frequency data.
When a problem is difficult and doesn’t want to go away, the best folks need to throw eyes on it to cut the L and bring back the P.
It also is very effective in training technicians to show them exactly the sequence of events which caused things to happen the way they did.
Every data point a controller recorded and SCADAScope collected as a time series.
For example, turbine pitch angle, every single position, one after another.
Yes, in CSV or image of the graph.
Separately, this data is available in packaged format for enterprise data systems and historians if you wish to archive it.
Yes, it is extremely useful in root cause investigations.
Yes, the system looks at this data, and our experts look at this data to gain higher certainty about the insights we share.
No, SCADAScope Grapher is always included with any installation.
Yes. Our recommended protocol is downloading the data over FTP from the server. There is also a REST API to download it programmatically.
Yes, the data is available. And we recommend using the more aggregated and less frequent post processed trends and aggregates for your business intelligence.
Most BI softwares are not designed for 2000 samples per second. That being said, even Excel could graph a snapshot of this data in a pinch.
Between 50 samples per second to 9600 samples per second. It entirely depends on the asset and PLC you are working with.
Usually higher resolution data are sporadic event faults that are recorded on an interval or at a given trigger condition.